Cutting-edge technology in plastic extrusion for modern industries
Wiki Article
A Comprehensive Guide to the Process and Benefits of Plastic Extrusion
In the huge realm of manufacturing, plastic extrusion emerges as a essential and extremely efficient process. Altering raw plastic right into continual accounts, it caters to a wide variety of sectors with its amazing adaptability.Understanding the Essentials of Plastic Extrusion
While it might appear facility at initial look, the procedure of plastic extrusion is basically easy. The process begins with the feeding of plastic material, in the form of powders, pellets, or granules, right into a warmed barrel. The designed plastic is then cooled, solidified, and reduced right into preferred lengths, completing the procedure.The Technical Refine of Plastic Extrusion Explained
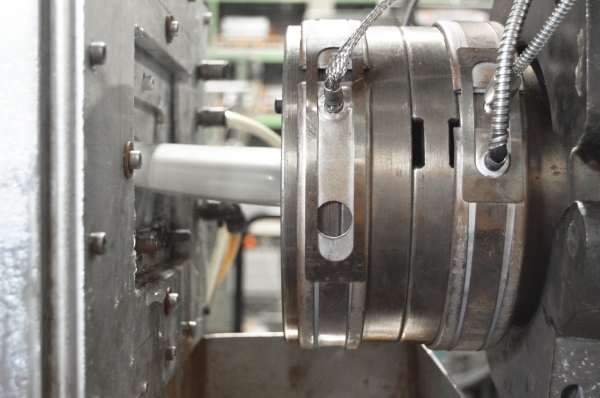
Sorts Of Plastic Suitable for Extrusion
The choice of the appropriate type of plastic is an important element of the extrusion procedure. Various plastics provide unique buildings, making them more suited to certain applications. Polyethylene, for instance, is typically utilized because of its affordable and very easy formability. It supplies excellent resistance to chemicals and dampness, making it suitable for items like tubes and containers. In a similar way, polypropylene is another prominent option because of its high melting point and resistance to tiredness. For even more robust applications, polystyrene and PVC (polyvinyl chloride) are typically picked for their toughness and longevity. These are usual options, the option ultimately depends on the specific needs of the product being produced. So, recognizing these plastic kinds can substantially boost the extrusion process.Contrasting Plastic Extrusion to Other Plastic Forming Approaches
Recognizing the types of plastic suitable for extrusion paves the way for a wider conversation on exactly how plastic extrusion stacks up versus various other plastic forming methods. Plastic extrusion is unmatched when it comes to creating have a peek at these guys constant profiles, such as seals, gaskets, and pipes. It also allows for a consistent cross-section along the length of the product.Secret Benefits of Plastic Extrusion in Manufacturing
In the realm of manufacturing, plastic extrusion uses lots of considerable advantages. One notable advantage is the cost-effectiveness of the process, which makes it a financially appealing production technique. Additionally, this technique offers exceptional product flexibility and enhanced production speed, therefore increasing total production performance.Cost-efficient Production Method
Plastic extrusion jumps to the forefront as a cost-effective production method in manufacturing. Furthermore, plastic extrusion requires less power than conventional manufacturing methods, contributing to lower operational expenses. Generally, the financial advantages make plastic extrusion an extremely attractive alternative in the manufacturing industry.

Superior Item Flexibility
Past the cost-effectiveness of plastic extrusion, an additional significant advantage in making lies in its superior product flexibility. This process permits the production of a broad array of products with varying layouts, shapes, and sizes, from easy plastic sheets to detailed accounts. The flexibility is connected to the extrusion pass away, which can be customized to generate the desired product layout. This makes plastic extrusion a perfect remedy for markets that require customized plastic parts, such as automobile, construction, and packaging. The ability to create diverse items is not just advantageous in conference particular market demands yet likewise in allowing producers to check out brand-new line of product with marginal capital expense. In significance, plastic extrusion's product versatility promotes innovation while boosting operational performance.Enhanced Manufacturing Rate
A substantial benefit of plastic extrusion lies in its boosted manufacturing rate. Few various other production processes can match the speed of plastic extrusion. Additionally, the capacity to maintain constant high-speed manufacturing without giving up product quality establishes plastic extrusion apart from various other techniques.Real-world Applications and Effects of Plastic Extrusion
In the realm of production, the method of plastic extrusion holds profound importance. This procedure is commonly used my sources in the manufacturing of a variety of items, such as plastic tubing, window structures, and weather removing. As a result, it greatly affects sectors like building and construction, packaging, and auto sectors. Its influence prolongs to daily things, from plastic bags to toothbrushes and non reusable cutlery. The economic benefit of plastic extrusion, mainly its high-volume check my blog and cost-efficient result, has actually reinvented manufacturing. The ecological impact of plastic waste remains an issue. The market is constantly aiming for innovations in recyclable and naturally degradable materials, showing a future where the benefits of plastic extrusion can be maintained without jeopardizing ecological sustainability.Final thought
In final thought, plastic extrusion is a extremely reliable and effective technique of changing raw materials into diverse products. It uses many advantages over other plastic developing approaches, consisting of cost-effectiveness, high outcome, minimal waste, and layout flexibility. Its influence is profoundly really felt in various markets such as building, automobile, and consumer products, making it a pivotal procedure in today's manufacturing landscape.Delving much deeper into the technical procedure of plastic extrusion, it starts with the selection of the proper plastic product. Once cooled down, the plastic is cut right into the called for lengths or wound onto reels if the item is a plastic movie or sheet - plastic extrusion. Comparing Plastic Extrusion to Various Other Plastic Forming Methods
Recognizing the kinds of plastic appropriate for extrusion paves the method for a more comprehensive discussion on how plastic extrusion piles up versus various other plastic developing methods. Couple of other production processes can match the speed of plastic extrusion.
Report this wiki page